MP35N Torx Screws
MP35N Torx Screws
MP35N Torx screws are known for their extraordinary strength and are the strongest screws we offer at RAYCHIN. MP35N screws owe their extraordinary strength to a unique alloy combination of nickel, cobalt, chrome and molybdenum and have ultimate tensile strengths that range from 227 ksi to 294 ksi (with age hardening).
Beyond the strength of MP35N Torx screws, they are also exhibit good corrosion resistance and can resist most mineral acids, hydrogen sulfide, seawater and salt spray environments.
MP35N Torx screws are also resistant to high temperature oxidation and could operate in environments up to 800°F and still maintain much of its strength.
One of the highest strength alloys available to industry
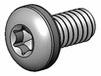
· Extreme high strength properties up to 300 ksi ultimate tensile.
· Good in moderately elevated temperatures of 800°F.
· Moderate corrosion resistance.
· MP35N Chemistry, specs, and heat treatments
· Datasheet for MP35N
· MP35N Torx screw features and benefits
Applications where MP35N Torx screws are often found are: aerospace, defense, marine, chemical processing, oil and gas and medical.
Resources: MP35N Torque Spec
Screw Types: 12 Point Screws, Button Head Cap Screws, Flat Head Screws, Hex Cap Screws, Pan Head Screws, Set Screws, Socket Head Cap Screws, Tamper Resistant Security Screws, Torx Screws
MP35N Torx Screw Features and Benefits
MP35N Torx screws are characterized by a 6-point star-shaped pattern, also called a star drive, spined socket or hexalobular (ISO 10664). Where Phillips heads were designed to cause the driver to cam-out (prevent overtightening), Torx screws were designed resist cam-out. This feature allows MP35N Torx screws to provide increased torque as well as better torque transfer between driver and fasteners. This feature also helps to reduce wear on driver bits.
MP35N Torx Screw Advantages
· Resistant to cam out (process by which a screwdriver slips out of the head)
· MP35N Torx screws are more difficult to strip
· Increased tamper resistance as a star driver isn’t as common
· Driver insert is less susceptible to damage when over torqued than Allen head
MP35N Chemistry, Specs and Heat Treatments
Heat Treating & Aging: MP35N is usually supplied in heat treated and cold drawn condition AMS 5844. In this state the MP35N can be worked into the desired fastener form and aged to the AMS 5845 specification. Once aged, the MP35N material could achieve it full strength potential.
MP35N Specifications: AMS 5844, AMS 5845, AMS7468, ASTM F562, NACE MR0175
MP35M | Ni | Co | Cr | Mo |
Typical% | 35 | 35 | 20 | 10 |
MP35N Mechanical Data (Dependent of Part Size)
Guaranteed Minimum Properties | Nominal Properties |
| USt(%) | Yield Strength (0.2%) ksi | Elongation (%4D) | RA(%)) | HRC | UTS(kis) | Yield Strength (0.2%) ksi | Elongation (%40) | RA(%) | HRC |
MP35N Cold Dg Full Strength | 260 | 230 | 8 | 35 | 44 min | 285 | 275 | 9 | 45 | 50 |
MP35N Corrosion Data
Media | Corrosion Resistance | Media | Corrosion Resistance |
Nitric Acid | Good | Sulfuric Acid | Good |
Phosphoric Acid | Good | Acetic Acid | Excellent |
Sodium Hydroxide | Good | Salt Spray (NaCl) | Excellent |
Sea Water | Excellent | SourOil/Gas | Excellent |